King George Hub Phase C is a 371-suite development located at the King George Station in Surrey, BC. The project has 34 floors above grade and a four-floor below-grade parkade. The conditioned gross floor area of the project is 295,206 ft2 with a further 101,874 ft2 of underground parkade area.
The project is mandated to connect to the Surrey District Energy Scheme, also known as community or neighborhood energy. The system distributes heat (thermal) energy, typically in the form of hot water, from a central energy center through a network of closed-loop underground pipes to individual customer buildings. The Surrey district energy system interfaces indirectly via heat exchangers with the buildings’ space heating and domestic hot water systems. No other heat sources are required.
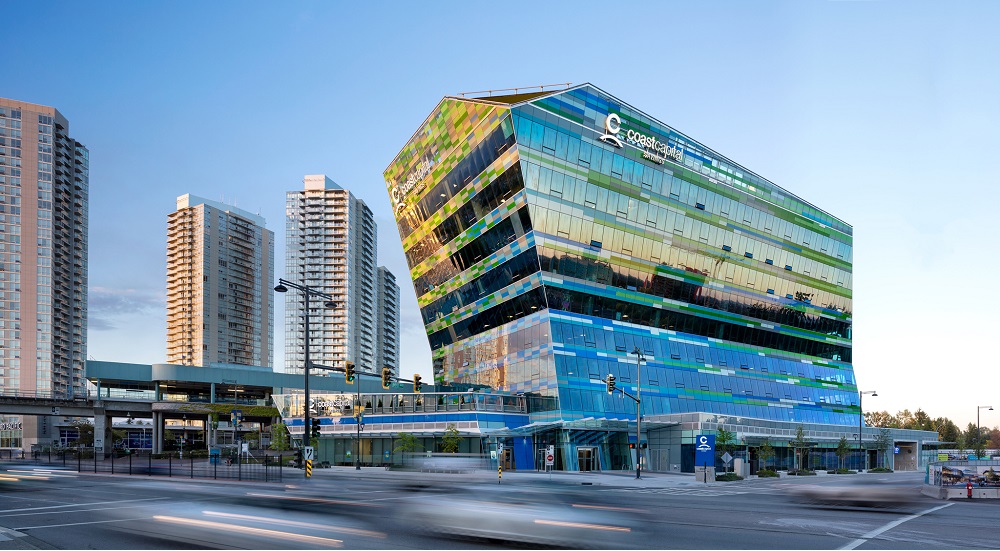
Some Advantages of District Energy
District energy systems offer many benefits:
For Customers
- Reliability, convenience, and comfort
- Lower capital, operations, and maintenance costs
- Stable prices, competitive rates
- Worry-free, simplified operations
For Developers
- Increased marketability
- Space savings, design flexibility
- Cost-effective solution to new building standards
For the City and Community
- Energy dollars stay in the community
- Improved energy efficiency
- Energy security, fuel flexibility
- Awareness of energy sustainability
For the Environment
- Reduced energy consumption
- Cleaner air
- Greener future
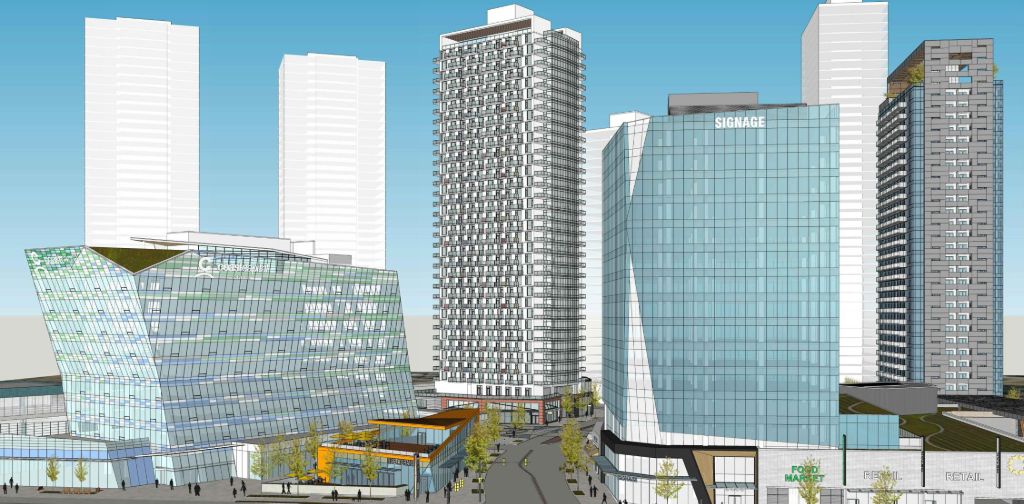
The Project Scope
Edge Consultants provided energy modelling services to demonstrate compliance with ASHRAE 90.1-2010 Energy Standard for Buildings Except Low-Rise Residential Buildings via the ECB (Energy Cost Budget) method.
Using the ASHRAE 90.1-2010 ECB methodology, The Edge team used IES Virtual Environment (Energy modelling software) to calculate the design energy cost for the proposed building design and to calculate the energy cost budget for a budget building design. In the budget building design, which is a variant of the proposed building design, all mandatory and prescriptive requirements of the ASHRAE 90.1-2010 standard were applied. The energy cost budget model represents the building as if it complied with the prescriptive requirements of the standard. The design energy cost for the proposed design cannot exceed the energy cost budget. For example, if the budget (code complaint design) model utility costs from the model equate to $20,000 per year, the proposed building model annual utility costs must be less than $20,000 per year to demonstrate compliance.
The benefit of the ECB compliance path is that it considers the overall performance of the building as an integrated system and in doing so enables the design team to make decisions that optimize the design based on interactions among its architectural, electrical and mechanical systems.
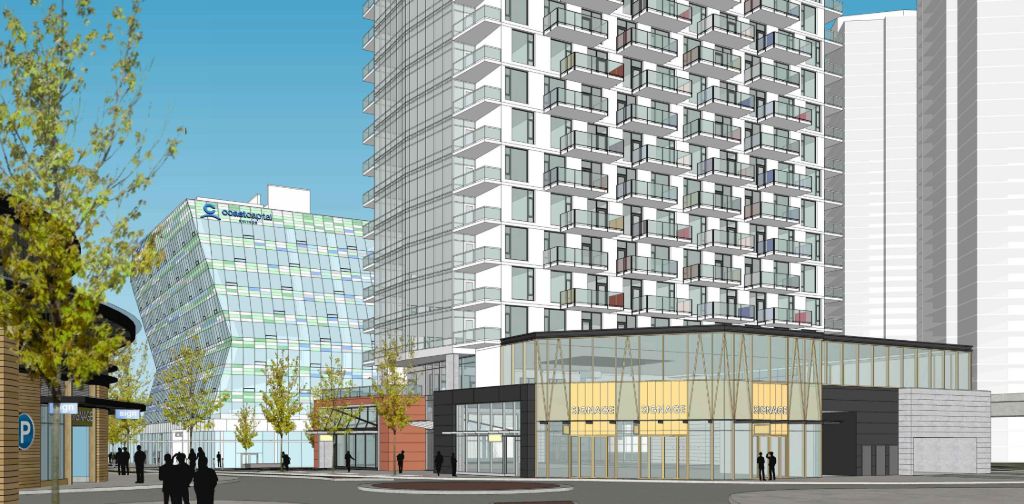
Mechanical System
The proposed mechanical HVAC system comprised of fan coil units with heating/cooling changeover coils. The heating water is supplied by the city of Surrey’s District Energy System (DES). Cooling is provided by Air-Cooled chillers.
Design Team
PCI – Client
MCM – Architect
TD Systems – Mechanical
Edge Consultants – Energy Modelling
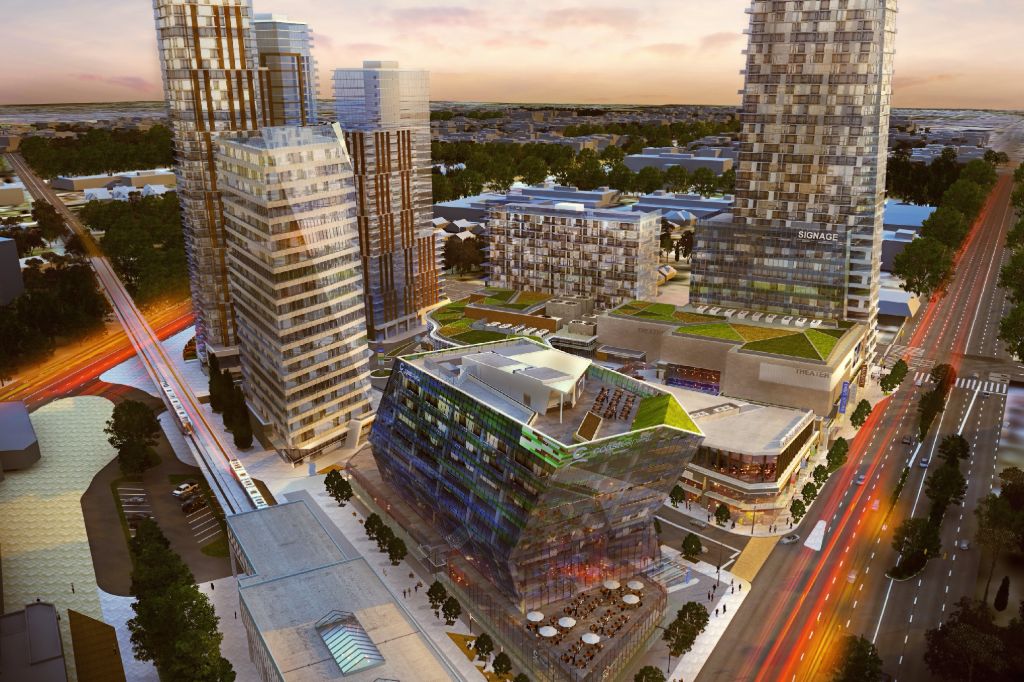