Airtightness is a measure of the resistance of a building’s envelope to infiltration when ventilators (windows, doors, roof light etc.) are closed. Infiltration is the unintentional or accidental introduction of outside air into a building, typically through cracks in the building envelope. A building envelope includes all components of a building that separate the indoors from the outdoors e.g. exterior walls, windows, doors. Airtightness is expressed in terms of the leakage airflow rate through the building envelope at a given pressure, divided by either:
- Heated building volume, measured in air changes per hour
- Envelope area called the air permeability, measured in L/(s.m2)
The greater the airtightness across the envelope at a given reference pressure, the lower the infiltration rate.
Airtightness within a building is an essential facet of building design. Air leakage through a building’s envelope can have a considerable impact on energy consumption and tenant comfort. It is important that sufficient attention be given to airtightness during the design stage, oftentimes it is overlooked. A whole building airtightness test measures how easily air can leak through the building’s enclosure.
The airtightness testing takes place during construction stages, but time and consideration should be given during the design stages to ensure that your project will achieve the desired/required results.
As energy modelers, we carry out comprehensive analysis on building energy use that considers how energy is produced, used, and lost. Energy modelers play their role in the design stage of a project and aim to predict as accurately as possible a building’s energy performance once constructed and occupied. Airtightness of a building is one of many elements considered in energy modelling. Increased airtightness in a building will result in increased energy performance, which will be explained later in this article.
Every building is constructed using several building assemblies such as walls, windows, and roofs. Determining an assembly’s exact infiltration rate can be difficult as it is a variable that is influenced by several factors (outdoor/indoor temperature differences, humidity, mechanical systems, to name but a few), and requires detailed calculations. The infiltration is also a variable, but it is recommended that fixed infiltration rates be applied to energy models. Applying a constant value aligns with the National Energy Code for Canada Buildings (NECB) 2015. NECB 2015 defines constant limits for air leakage rate through specific assembly types.
Why carry out an Airtightness Test?
Airtightness testing is a Step Code requirement, as outlined later in this article, aside from this there are many benefits of designing your building with increased airtightness. Some of the benefits of having improved airtightness include:
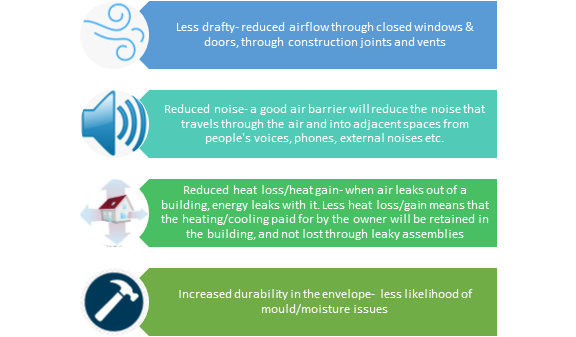
An Air Barrier stops air leakage through a building. Air leakage can carry moisture, heat or cold. There can be multiple air barriers on an assembly. To function as an effective air barrier, they should be:
- Air impermeable
- Continuous
- Durable
- Stiff and strong
Increasing building airtightness is a good move towards increasing the overall building energy efficiency. Airtightness is part of an enclosure/fabric first approach. When combined with efficient heating, cooling, and ventilation systems your project takes steps towards being a high-performance building.
The British Columbian (BC) Energy Step Code
For municipalities that decide to adopt the BC Energy Step Code, airtightness testing is mandatory for all residential and non-residential projects. Currently 14 municipalities in the Lower Mainland have adopted the BC Energy Step Code, with two other municipalities in the consultation phase.
The BC Building Code regulates building in two main categories: simple buildings and complex buildings, commonly referred to as Part 9 and Part 3 buildings.
Part 3 Buildings
Part 3 buildings typically comprise of all buildings over three storeys in height or over 600m2 in footprint. Part 3 buildings are generally intended for public gatherings, residential care, detention, or high-hazard industrial activities. Office towers and shopping malls are examples of Part 3 buildings.
Under all steps of the Step Code, Part 3 building types require whole building airtightness testing, as well as an energy model. One airtightness test is obligatory once the air barrier system is complete. Part 3 building types do not have a specified minimum air leakage rate that must be achieved when the airtightness test is carried out, the Energy Step Code simply requires that a test be completed. For steps 2-4 of the step code, the airtightness value achieved through testing must be reinserted back into the energy model (see section 10.2.3.4 of the BC Building Code, found here). Until the air leakage rate of a building is determined from an airtightness test, “an air leakage rate determined in accordance with the City of Vancouver Energy Modelling Guidelines shall be used” in the energy model, these guidelines can be found here.
The Process
Whole building airtightness testing requires coordination from the full integrated design team. It is recommended that airtightness mock-ups are made during the construction process. The earlier the engagement of the envelope consultant and contractor in this process, the better. This way feedback on constructability can be received earlier and planned out in full.
When initially engaging in discussions on air barrier testing, it is recommended that design teams:
- Minimize complex transition details
- Focus on a few details and refine them
- Develop specifications for airtightness requirements from the contractor team
As stated in the BC Building Code and the Vancouver Building by Laws materials used for the air barrier must “have an air leakage characteristic not greater than 0.02 L/s.m2 measured at an air pressure difference of 75 Pa” or alternatively the material must conform to the CAN/ULC-S741, “Air Barrier Materials- Specification.” In addition to the air leakage rate, other factors such as durability, cost, material chemical compatibility, adhesion and constructability should also be considered in material selection. These considerations can be worked out early when the integrated design team is engaged in the airtightness planning & testing process.
When carrying out the air barrier test itself, there are two standards within the BC Building Code that can be used for Part 3 buildings:
ASTM E 779- Standard Test Method for Determining Air Leakage Rate by Fan Pressurization
USACE Version 3- Air Leakage Test Protocol for Building Envelopes
Both standards are similar and are based around the same procedures; the USACE standard was built off the ASTM E 779 standard.
Completion of mid-construction building airtightness tests are not required by code but are often recommended to ensure that your project is in line to succeed in meeting the intended airtightness targets.
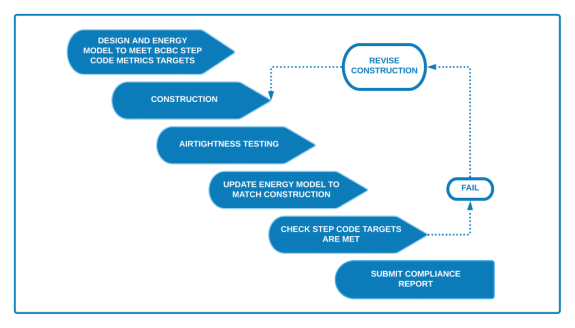
The minimum requirement for compliance is that airtightness testing is completed after the building construction is completed- after inspections and prior to occupancy.
Part 9 Buildings
Part 9 buildings include most buildings three storeys and under in height and with a footprint of 600m2 or less. They are typically small buildings intended for residential, commercial, or medium-to-low hazard industrial activities. A single-family home is an example of a Part 9 building. For Part 9 buildings there are different minimum airtightness rates that must be achieved depending on what step of the Step Code is being applied. Step 1 does not have a specified minimum air leakage rate, whereas Steps 2-5 do.
The image below shows the maximum allowable air leakage rates for each step of the Step Code for Part 9 buildings. The air leakage rate below is measured in air changes per hour (ACH) the subscript denotes the pressure at which the testing takes place, in this case it is 50 Pascals of pressure.
Completion of mid-construction building airtightness tests can be particularly useful for Part 9 buildings when there are maximum air leakage rates that your building cannot exceed.
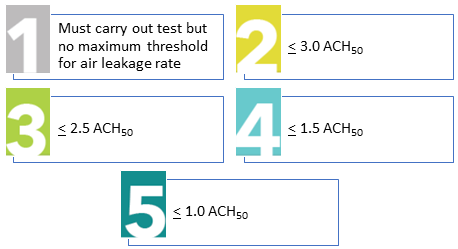
Conclusion
Increased building airtightness is one of many steps that are being taken to increase the energy performance. Airtightness targets are being introduced across the province through the BC Step Code- similar trends can be seen in the building industry world-wide. Introduction of airtightness targets is becoming common place; they are being added to building codes and energy programs. Owners are becoming more aware of the benefits of better performing buildings. Owners are striving for more energy efficient buildings to reduce operational costs, increase building lifespan and durability, increase tenant comfort, and improve indoor air quality. Air tightness testing provides a quantitative metric that verifies design and construction methods were successful in achieving an airtight building.
If you want to learn more about airtightness testing and the Step Code, check out their website here.
For more information on the BC Building Code, and the code itself can be found here.
The City of Vancouver Energy Modelling Guidelines can be found here.
The standards used in the BC Building Code for airtightness testing can be found here and here.