What is “Quality”?
The International Organization for Standardization (ISO) defines “Quality” as “the degree to which a set of inherent characteristics fulfills a requirement,” and “requirement” as “a need or expectation that is stated, generally implied or obligatory.” The Oxford English Dictionary defines quality as “the standard of something when it is compared to other things like it; how good or bad something is.”
Quality is a lot more than just describing a product or service as “good.” Quality is about maximizing productivity and meeting (and exceeding) customer’s and client’s expectations through the delivery of products and services. Every organization, of every size, across all industries benefit from ensuring organizational quality in all processes and procedures. Quality is an approach that should be a central goal of all organizations.
Although quality departments do exist in many companies, quality itself is not a specific discipline or program. Quality is not completed when you achieve a certain target. Quality should live within every aspect of an organization and be part of the company’s core values, it is a continuous process with no end point. We at Edge have always taken quality very seriously, and as our team grows, we are realizing more and more the importance of having quality procedures in place for new employees, allowing the whole team to be on the same page regarding standards and quality of work expectations from the outset.
Quality starts at project inception. Customer, stakeholder, employee, and business needs, wants and expectations must be considered from the outset. This ensures delivery of a quality product or service that all parties will be satisfied with.
Who is responsible for Quality?
William Edwards Deming, one of the leading management thinkers in the field of quality, once stated that “quality is everyone’s responsibility”, signifying that quality is something that should be universal in an organization. It should be a central and common goal of an organization, every employee, regardless of title, should take responsibility in ensuring quality is continuously upheld in the work they do. This being said, ultimately leadership needs to pave the way for a culture of quality and demonstrate their quality commitment by providing the required tools to support quality initiatives throughout the organization. Leadership should clearly communicate the quality values of the organization and lead by example in implementing them. Fostering a culture of quality in an organization makes for a more productive work environment where employees are encouraged to carry out cross-functional work and share ideas. Quality should be viewed by all as something that builds positive change.
Some organizations will have defined quality departments and/or individuals in roles dedicated to ensuring quality across the company (e.g., Quality Engineers, Quality Managers, Quality Control Inspectors). Regardless of whether there is a role dedicated specifically to Quality in an organization, it is the responsibility of every employee to ensure that they are implementing the company’s quality management procedures in their own work. Quality is a companywide process. Without buy-in and action from people on an individual level, a culture of quality cannot be adopted effectively or efficiently. Everyone has a role to play when it comes to quality.
Organizational quality is truly embraced by all when there is an environment in which employees go beyond following the standard quality guidelines; they discuss quality, its importance and continuously make quality-driven decisions in their work.
From an Engineering and legal perspective here in British Columbia (BC), the Engineers and Geoscientists of BC (EGBC) is the “regulatory and licensing body for the engineering and geoscience professions in BC. To protect the public, Engineers and Geoscientists BC establishes, monitors, and enforces standards for the qualification and practice of Professional Registrants.” The EGBC provides practice resources to Professional Registrants to assist engineering professionals in meeting their professional and ethical obligations under the Professional Governance Act, S.B.C. 2018 and Bylaws. One category of these practice resources is Guides to quality management standards, which explain the standards of practice, conduct, and competence for quality management in professional activities.
What is Quality Management?
Quality management sets clear criteria of what is to be done to achieve results, it is made up of several elements including quality planning, quality improvement, quality control and quality assurance. Quality management ensures consistency not just in products and services, but also in the methods and means used to provide and deliver the product/service. The goal of Quality Management is to deliver a high-quality product or service, on a continuous basis.
- Quality Planning – According to ISO 10005:2005 quality planning involves creating a quality plan that provides a means of relating specific requirements of the process, product, project, or contract to work methods and practices that support product realization. It requires you to take all the information available at the beginning of the project and figuring out how you will measure quality and prevent defects.
- Quality Improvement – Anything that results in a beneficial change in the quality performance of a product or service.
- Quality Control (QC) – is defined by the Project Management Body of Knowledge (PMBOK) as the measurement of outputs to determine whether they meet the accepted criteria.
- Quality Assurance (QA) – is defined by the PMBOK as analyzation of the processes and systems that are producing the outputs i.e., measurement of the systems.
QC and QA can often be mixed up. QC processes are in place to remove defects, QA procedures are in place to improve your systems. Customer, employee, and stakeholder feedback should be gathered and monitored on an ongoing basis and relevant changes arising from feedback should be incorporated into company processes. QC can be something as small as reading a report and fixing a spelling mistake, or something as big as equipment testing. Checking work (self-checks or checks by others) is another example of QC. EGBC highlight in their Quality Guidelines that “for checks to be effective, proper planning must occur before professional engineering or professional geoscience work is carried out.” Examples of QA activities include following a process checklist or conducting a project audit. QC and QA processes feed into each other. QC items can result in quality improvement measures that follow in QA process changes. QA processes are created with the intention of preventing issues arising during the QC process. Implementing QA and QC procedures mean you are applying a quality standard to your work.
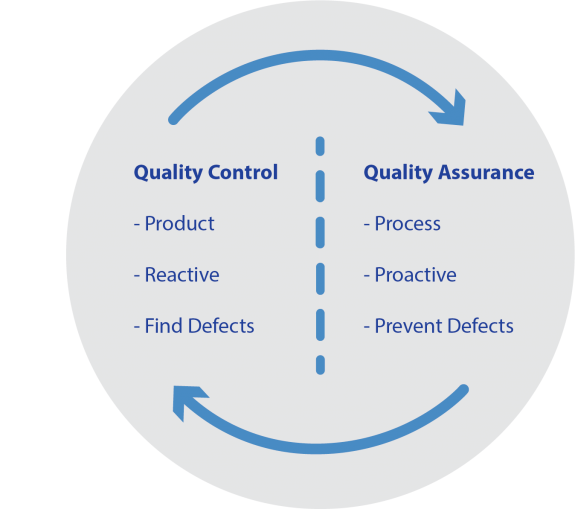
Mapping out internal processes and having an owner responsible for each step along the way ensures that everyone within the organization knows and understands how the internal quality management procedures take place. Clearly defining these procedures increases organizational efficiency, thus saving time and money.
Organizational QC and QA documents should be developed by teams/responsible parties to track and measure the quality of deliverables. These documents should be kept on record should they need to be checked down the line. Having QC/QA documents and processes in place ensures that proper consideration is being given to quality from the outset and that people take ownership for the work being done. QC/QA documents prove extremely valuable should issues or questions be raised. The EGBC Quality Guidelines outline that the retention of project documents may also allow to “resolve issues, meet legal and regulatory requirements, document decision-making procedures, defend claims, facilitate undertaking future work, and/or make intellectual property readily retrievable for future solutions”. The QA/QC project documents map product/service development, record any issues, note how they were resolved, and can be referred back to at any point in time.
Energy Modelling and Quality Management
As energy modelers, we use software to simulate whole building energy use across a year and demonstrate that a project meets the relevant energy codes or a predetermined performance standard. Buildings are made up of many large, complex, interdependent systems with interacting components. These systems and components are influenced by factors such as occupant behavior and external weather. With so many moving parts feeding into a single building energy model, there are many areas where mistakes can be made, as a result it is imperative that we have defined quality management procedures in place. Examples of QC in energy modelling include cross checking that the energy model inputs reflect the relevant architectural, mechanical, and electrical design parameters, or carrying out manual calculations to verify figures produced by the simulation software. These procedures ensure the work we produce is accurate and of a high standard.
The City of Vancouver’s Energy Modelling Guidelines and The US Environmental Protection Agency’s (EPA) ENERGY STAR® Multifamily High Rise Program Simulation Guidelines are examples of overarching energy modelling quality assurance documents. These Energy Modelling Guidelines ensure that energy modelers working on projects within a certain jurisdiction are applying the same methodologies and assumptions to their work. Other such industry standards that apply to energy modelling include:
- ASHRAE 90.1 Section 11 and Appendix G
- National Energy Code of Canada for Buildings (NECB) Part 8
- Canadian Standards Association (CSA) C873 Series 15
The documents listed above are industry-wide quality assurance documents. They set the minimum standards that projects must reach to achieve the relevant project approval.
Implementing quality management procedures ensures consistency and reliability with each iteration of a product or service. This drives efficiency, which in turn drives company profits.
Why is Quality and Organizational Quality Management important?
Implementing quality management procedures in an organization puts emphasis on delivering high-quality products and services that meet customer’s needs and wants. High levels of customer satisfaction results in customer loyalty. If customers or clients receive an above-and-beyond quality product, they will often remain loyal even if their product comes at an increased cost. Take a look at Apple: Apple devices are often more expensive than their competing counterparts, but they remain one of the market leaders because of their quality products. Quality is often the differentiator that sets apart competing organizations who offer similar products or services.
Below are some of the high-level benefits of having clear, defined quality processes.
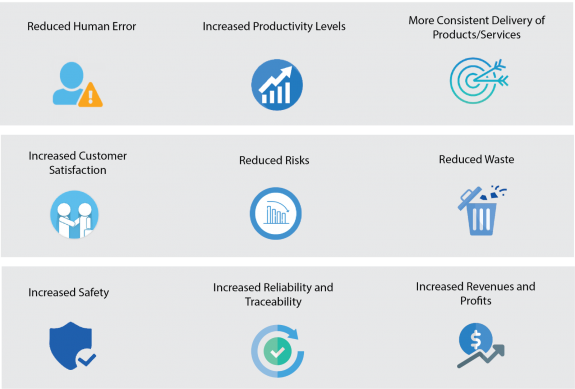
Looking specifically at engineering and energy modelling – if we did not apply internal quality management processes to the work we produce, it is possible that poor quality energy modelling projects could mistakenly gain approval if project parameters and assumptions do not follow the correct quality control procedures. Cross checks between energy model inputs and design parameters need to be continuously carried out to ensure consistency, accuracy and that the energy model is in fact true to the most recent design. Mistakes that are made in engineering design stage can prove costly later in projects. If construction begins and design calculations have been inaccurate, safety risks come into play. As engineering professionals, we have a responsibility to produce quality work, the more quality procedures we apply to our work the more we can guarantee high quality products and services.
The creation and implementation of quality management procedures can take time, especially at the outset. Ensuring the correct processes are in place and aiming to guarantee consistency along each step of your product/service pathway does have a cost, but the cost of not implementing these procedures is far greater. The cost of poor quality has been assumed to be between 4-5% of an organization’s annual revenue. Once quality management procedures have been defined, the typically run simultaneously alongside other organizational processes.
Conclusion
Quality management is vital not just in engineering and energy modelling, but in every industry across the board. Achieving quality is an iterative process with a continuously moving target. There is essentially no finish line when it comes to quality- there is always room for further improvement. There should be no single person responsibility for carrying quality in an organization – it is a responsibility that should be shared by all. Companies should always strive for better when it comes to quality. Processes should be reviewed periodically, and conversations should be had to see if anything can be improved upon. Everyone should look at their own processes with quality management in mind and think about ways they can bring about positive change within their organization.
For more resources on quality management please check out the links below: