The Legacy Holdings development is a core and shell industrial warehouse building located at 3853 191st street in Surrey, BC. The construction has a total of 85,196 ft2 gross floor area consisting of a one-story building, divided into three warehouse units. Allowances have been made for a future mezzanine level of 9,413 ft2 to accommodate office spaces in each of the warehouse units.
The buildings have been designed with mechanical HVAC (Heating, Ventilation, and Air Conditioning) equipment to maintain suitable temperatures in the warehouse units. The HVAC equipment required for the future office spaces is not included in the development as it is expected to be completed during future tenant improvement. This approach is typical for core and shell developments as the specifics relating to the future use of office space is not known; design will vary based on occupancy rates and schedule.
Scope of Work
For this project, Edge Consultants demonstrated how the proposed development meets compliance with ASHRAE 90.1-2016 Energy Standard for Buildings Except Low-Rise Residential Buildings via the ECB (Energy Cost Budget) compliance path as referenced under the British Columbia building code 2018.
Benefits of the Performance Model Approach
Engaging Edge Consultants to complete an energy performance model for this development had significant financial benefits for the client. By following the ECB compliance path rather than the prescriptive compliance path, the project had much more flexibility in design decisions which provided the potential to make financial savings. This is the case for projects in general that follow the ECB path.
If the project followed the prescriptive path, each component of the building design would be strictly defined by the energy compliance standard. That means the level of insulation in the walls, roof, floors would be fixed by a minimum thermal performance requirement. The requirement for glazing performance would follow a similar approach. HVAC equipment would be required to meet minimum efficiencies and any approvement above these efficiencies is not incentivized.
On the other hand, using the ECB compliance path, each component of the building design is not strictly defined, and the design team has the flexibility to make decisions that benefit the project. For example, insulation can be added to the roof to reduce space heating energy requirement. This can enable the project to remove the requirement for floor insulation. Similarly, there is a benefit to increasing the efficiency of HVAC equipment above the minimum requirements as this can reduce energy consumed for heating and cooling. The improved mechanical efficiencies can enable the team to lower the performance of other building components, such as the glazing for example, and still be compliant with energy requirements.
Edge Consultants are experienced with completing energy performance models with the client’s interests in mind. Edge can discuss individual design components with the team and run various scenarios to find the best solution for the client. This approach can ensure the design is both compliant with requirements and the client is not over-spending on certain areas of design unnecessarily. Using the energy performance model approach, rather than a relevant prescriptive compliance path, enables the client to make significant financial savings on a project.
Proposed Modelled Construction
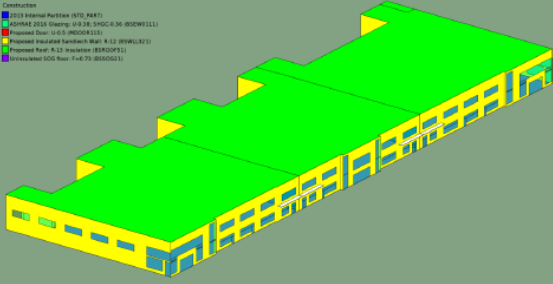
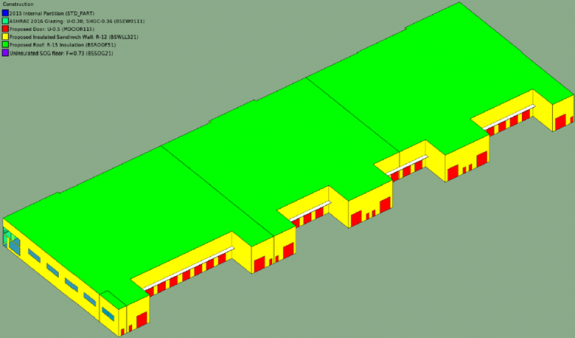
Design Team
Orion Construction (Project manager)
D.Force Design Inc. (Architect)
Blueridge Engineering Ltd. (Mechanical)
Opal Engineering (Electrical)
Edge Consultants (Energy Modeling)